Pipe type bus bar installation instructions 1 scope of application Pipe type bus this instruction is suitable for substation 500kV and below voltage installation. The 2 compilation basis Table 2-1 reference standard and specification name Serial number Standard and specification name Authority 1 "Standard" electric equipment installation engineering construction and acceptance of GBJ149-90 bus device Ministry of Construction of the People's Republic of China 2 "Electric equipment installation standard" for hand over test of electric equipment engineering GB50150-2006 The people's Republic of China National Development and Reform Commission 3 "Preventive test code for electric power equipment" Q/CSG 1 0007-2004 China Southern Grid Corp 4 "110kV~500kV power transmission and substation engineering quality inspection and evaluation standards" Q/CSG 10017.2-2007 China Southern Grid Corp 5 "Substation NOSA facilities standards" Q/CSG10001-2004 China Southern Grid Corp 6 "China Southern power grid construction process control specification" Q/CSG11105.2-2008 China Southern Grid Corp 7 "China Southern Grid Corp ten anti accident measures" China Southern Grid Corp 8 "Code of safety operation in power" (part of substation) DL5009.3-1997 Ministry of power industry of the people's Republic of China 9 "Electrical safety regulations" (power plant and substation electrical part) DL 408-91 The energy department of the people's Republic of China 10 Construction drawings XX Electric Power Design Institute 3 processes 3.1 operation (step) flow chart
Figure 3-1 operation flow chart 4 security risk analysis and control Table 4-1 risk analysis and prevention measures of the safety check list Serial number Safety risk Pre control measures Inspection results 1 Lifting pipe bus to bus swing damage to equipment and personnel The bus should be tied at both ends of the cable wind rope guide 2 Pipe base welding arc burns the skin, eyes Welding personnel must wear protective equipment when welding 3 Workers working on the bus ride The use of aerial work platform truck 4 Equipment and motor with no ground crane, argon arc welding Used to meet the requirements of wire, reliable grounding 5 Falling Construction personnel required to fasten the safety belt, wear safety helmet 6 Please carefully check and signature confirmation, your signature means will bear the responsibility of safety and quality of the corresponding The construction unit inspection: supervision unit inspection: Date: date: Note: the risks and control measures to improve the fill "√", the risk control measures are not perfect and fill out the "X", then fill out the "-" there is no risk, no check blank. 5 ready The 5.1 Manning Equipped with Table 5-1 Process name The number of recommended work Responsible for the number Monitoring the number Preparation of construction foundation check 5 1 - Mother, inspection, correction of liner tube 4 1 - Pipe material processing; welding, welding wire, pipe cleaning 5 1 1 Welding 3 1 - Post insulators, hardware check 4 1 - Post insulators, hardware installation 6 1 1 Tube bus transportation in place 4 1 - Lifting adjustment 8 1 1 Note: the numbers of workers according to the specific engineering scale with. The 5.2 main instruments and instrument configuration Table 5-2 for the main instruments and instrument configuration table Serial number Name Specifications / No. Company Number Remarks 1 Crane 25T/35T Table 2 2 Argon arc welding machine 380V/400A Table 2 3 Bus groove machine 80 - 250 mm Table 1 4 Metal cutting machine Table 1 5 Flame welding, gas cutting torch Set 1 6 Bench drill Table 1 7 Motor winch 3T Table 1 8 A wire rope 12 16M Yes 1 9 Torque wrench Set 2 10 Ratchet wrench The 4 11 Camisole 3T 8M Article 6 12 Crowbar Root 4 13 Level ruler 400mm The 1 14 Level Set 1 15 Steel tape 50 meters The 1 16 Other commonly used tools / Set 1 Note: the main instruments and instrument according to specific project scale with. 6 operations method 6.1 construction preparation 6.1.1 Technology: Technology for construction personnel work according to the procedures, installation instructions, drawings, manufacturers design requirements and construction measures, disclosure should be targeted; 6.1.2 staff: technical director, responsible for the installation, safety quality responsible person and technical workers; 6.1.3 equipment preparation: according to the construction requirements for equipment and the inspection and maintenance of the property and the state; Preparation of 6.1.4 construction materials: pipe base, post insulator, fittings, steel, steel plate, bolts etc.. 6.2 bus pillar insulator 6.2.1 in the earth pillar insulator and tube bus support and the fixed clamp assembly, in order to reduce the amount of work high above the ground. The 6.2.2 insulator should use the crane hoisting, lifting nylon rope lashing. Each bottle top level three phase error should be less than 3 mm, single-phase entire pillar insulator top horizontal error should not exceed 10 mm. The 6.3 tubular busbar processing 6.3.1 welding pipe bus welders shall be qualified in the bus, and before construction, must pass the examination qualified welder. Electrodes should be used wire and tube mother the same material, the tube bus should be welded specimen inspection before welding. Test should meet the following requirements: (1) surface and the fracture surface of the weld inspection, shall not be depressed, cracks, lack of fusion, incomplete welding defects; (2) the X light weld NDT and qualified; (3) the weld DC resistance measurement, and its value should be less than the resistance of raw metal with section, the same length value; (4) the weld tensile strength test, the average minimum tensile strength of the welded joints shall not be less than 75% of the raw material; (5) specimens of welding materials, welding joint type, location, technology should be the same as the actual construction. 6.3.2 to prevent weld porosity, slag inclusion and oxidation and other defects, welding must be removed before welding in the welding area of the oil, rust, dirt, oxide and other impurities, until the appearance of gloss. Mother cut off before the 6.3.3 pipe should be based on each bus cross-section diagram measured the length of welding pipe base, the bus welding parts from fixed line pipe base clip distance of not less than 50mm, and avoid the interval T clip, a static contact position isolating switch. Cut off the mouth should be smooth, and the vertical axis, welding good each pipe shall be marked with the label of mother. 6.3.4 each pipe joint groove machine processing groove, groove should be smooth, uniform, no burr. Tube bus groove type and butt size as shown in Figure 6-1, 6-1.
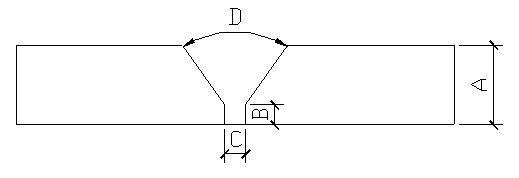
Fig. 6 - 1 tube bus groove Table 6 - 1 busbar groove and butt size The pipe wall thickness (mm) A Groove form Groove angle D Blunt edge (mm) B Clearance (mm) C 6 10 V 60 75 1.5 2.5 3--6 6.3.5 support working location: 10 [22 × 6m channel linear welding, and welding steel roller on inner side of a slot (every 2M1 on), to ensure compliance with the channel steel and the rolling center line bending deviation of not more than 0.2%, center line deviation of not more than 0.5mm. In the notch each channel distance port at 200 mm corresponding sides are provided with 20 semicircular groove, used for placing aluminium rolling pulley. Support channel after processing more spacious grounds, straight flat, with sleeper pad height from the ground to 200 mm, the two sides of the support necessary for angle steel buried firmly fixed, roller central line bracket and highly to be used for instrument calibration control in a straight line and a plane. 6.4 welded tube bus 6.4.1 welding must be confirmed before the welding material grades, understanding its chemical composition, physical and chemical properties, so that the correct selection of welding material, welding operation before the first batch of welding test, according to the provisions of the specimen. 6.4.2 bus groove on both sides of the surface within the range of 50mm cleaning clean, there shall be no oxide film, water and oil; groove machining surface should be no burr and burr. 6.4.3 will be a tubular busbar has been placed in leveling for welding rail bracket on (horizontal error is controlled within 3mm), the first tube after alignment will be lined into, then the second pipes installed, two pipe butt gap type bus between the 3~5mm, and then looking for pipe line of direction and the horizontal type bus center. Confirm after alignment can be strengthened hole weld as fixed, and then use the special clamping tool rotating pipe base its flatness inspection, to meet the requirements after the assembly of a pipe, to ensure its bending migration should not be greater than 0.2%, the center line deviation should be less than 0.5mm. 6.4.4 each weld shall be a welding end, in addition to instant broken arc may stop, bus not before cooling after welding, not to move or force. 6.4.5 bus to complete timely point fixed, fixed and welding sequence as shown in Figure 6 - 2, 6 - 3 show.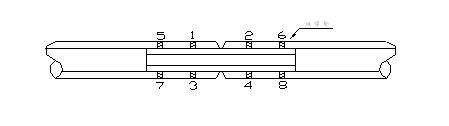
Figure 6 - 2 spot welding schematic diagram

Fig. 6 - 3 levels of fixed welding sequence 6.4.6 undercut depth shall not exceed the bus 10% of the wall thickness, and its total length shall not exceed the total length of the weld of the 20%. 6.4.7 tube type busbar butt weld parts of the distance post insulator bus plate edge should not be less than 50mm. 6.4.8 after welding the weld should be clean, smooth, workpiece due to combustion of black spot and welding the cloth or steel wire brush to clean all must be. Tube busbar welding should do a good job in the corresponding number, and stored in the multi point support, leveling and centering on the track. 6.5 tube bus bar installation 6.5.1 tubular busbar lifting should be installed before and good sealing end cover or terminal ball into the damping line in each section, the terminal ball should oil color paint. Note the dripping holes terminal ball should be down. 6.5.2 in the pipe base erection, the requirements of the application of conductive contact surface of sandpaper or wire brush to remove the oxide layer on the surface, wipe with a cloth clean oil, and then coated with grease can be used only for the installation of electric power. When lifting should be before the tube bus on the label for lifting, avoid the tube bus in place after the position is not correct. 6.5.3 in order to make the process of lifting pipe busbar bending deformation does not occur, should adopt multi point hoisting, in order to improve the accuracy of hoisting, lifting the general single span available two, two cross and above should be used three point hoisting. 6.5.4 tube bus before lifting, the pipe should be installed bus line clamp, a lifting, hoisting rope strength safety factor shall be not less than 5 times on the bus, tube securing points should be considered a skid proof and easy to release, rope angle should not exceed 120 degrees, the other should be added at the two ends of cable pipe base wind rope, so as not to tube mother and other equipment collision. Hoisting 6.5.5 support type bus: (1) the whole period of hoisting the tube bus, with long hanger for lifting. The mother root tube straightening good with a special fixture (no force can be free to take off), every 3 ~ 4m steel beam fixed on the hanger, hanging with the crane to the installation location. Insulator hanging or braced tube base installation, pipe and fittings are required to master the center center coincide. Supporting porcelain can be installed by theodolite and level alignment, ensure the horizontal and vertical. (2) to the level of inspection and adjustment phase and interphase distance error of busbar connection in place, expansion joints, according to the requirements of the drawings, adjust and fix the type line clamp, and pay attention to the distance between the phase expansion joint and the clamp and the pipe base distance, to meet the requirements, prevent the parent line heat extension and contraction. Die. 6.5.6 hanging tube type busbar lifting (1) should be strictly in accordance with design drawings assembled suspension insulator string, in strict accordance with the first root canal determine busbar lifting adjusting the length of all the insulator string, ensure equal insulator all tubular bus the same type of string. (2) the fixed hardware all tubular busbar by the first root tube busbar lifting fixed position all firmly into place, pay attention to the tubular busbar arch her back up. (3) the suspension insulator string lifting in place all, the tubular busbar and insulator reliable connection. Then the mother of the static tube hoisting method, smooth lifting pipe type bus. (4) hoisting preparation: layout of hoisting, lifting point is determined according to the pipe base form and the length of the suspension, and the same number of hanging points (3) and suspension when the angle (50 degrees), motor-driven winch fixation. Pipe base binding to use nylon slings, Lashing points for hanging point suspension insulator. (5) unified command by hand operation of the hoisting process, ensure pipe parent in the lifting process in a horizontal position. (6) near the suspension insulators in ascension pipe, stop electric winch, adjust the tube in tube mother mother force under static state, the tube center deviation mother can be adjusted through the flowers blue bolt. After the completion of the pipe base weld all guaranteed, and vertical elevation ≤ 5cm (rules 1.5 ‰ L, about 8cm).
7 measures of quality control and inspection standards 7.1 quality control measures The vertical center 7.1.1 civil architecture level position: in the pipe base before processing, must do the test of a full range of vertical center member, get accurate numerical, as numerical basis of piping. 7.1.2 single pipe before welding pipe straightness: mother in transport handling, lifting and other reasons, to the construction site of the tube bus have different degree of deformation, the tube straightening processing base. Processing and assembly of 7.1.3 pipe weld interface: mother mother pipe butt welding should be 30 ~ 40 degree bevel, 1.5 ~ 2mm blunt edge, mechanical processing, surface without burrs and flashes, interface on both sides must try to close, in order to improve the welding strength. 7.1.4 welding: must be placed on a roller bracket pipe base welding, on a flat surface, according to the length of pipe installation tube mother, mother will have the processing of each section on the welding bracket, the middle of the liner is required when in place, adjust the pipe line and level of mother, welding spot welding fixing, to review the pipe line and level of the mother, is correct before welding. Each weld to be cooled before moving. Available by special crane long hanging or multi-point support move, the whole root canal mother moved to hoisting position, smooth on the multi supporting the sleepers, correcting device using hydraulic of the whole root canal base alignment omni-directional, until it meets the requirements. Each weld need one-time welding completed, in case of power failure or failure to welder welding processing. 7.1.5 lifting pre arch treatment: before installation of pipe parent pre arch treatment, to ensure that the pipe base installation flatness. 7.2 quality control form Quality control form according to the XXXX table XXX. 7.3 inspection standard Quality inspection according to the Q/CSG 1007.2-2007 "110kV~500kV power transmission and substation engineering quality inspection and evaluation standards of second parts: substation electrical installation engineering" Q/CSG table 3.1.1, table 3.1.2, table 3.1.4, and shall comply with the standard requirements. |